

Daily Maintenance and Drive Methods for Welding Roller Racks
Release Time : 2025-01-03 View Count : 次Welding roller racks are essential for efficient and precise welding operations, particularly in seam welding. Proper daily maintenance ensures smooth performance and extends the equipment's service life. Additionally, selecting the right drive method is crucial for optimal performance. This article discusses essential maintenance practices and drive methods for welding roller racks.
MC
Daily Maintenance of Welding Roller Racks
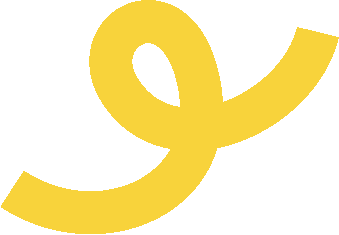
Maintaining a welding roller rack after each use is crucial to ensure its longevity and smooth operation. First, ensure the surrounding area is free from debris or obstacles that could interfere with the machine’s function. Once the system is powered on, run it without load to check for any unusual noises, vibrations, or odors, which could indicate potential issues.
Inspect all mechanical connections, particularly bolts, to ensure they are tight and secure. Loose bolts can cause instability, so they should be tightened before use. Also, check the guide rails for any debris and verify that the hydraulic system is functioning properly. The rollers should rotate smoothly, and any irregularities should be addressed promptly.
The welding roller rack should be installed in a dry, ventilated area, free from moisture and dust. It should also be protected from corrosive liquids and excessive vibrations. Additionally, ensure that the master and slave roller frames are properly aligned and at the same height. The frames should be positioned horizontally with their centerlines in a straight line.
During operation, the roller should fully contact the workpiece without touching welds or sharp edges. Avoid hitting the rollers when handling workpieces, as strong impacts can damage the machine or cause it to tip over if not properly secured.
MC
Seam Welding Machine Roller Drive Methods
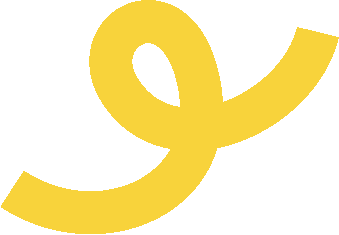
The drive system of a welding roller rack plays a significant role in the accuracy and efficiency of the welding process. A common drive method is using a constant-speed AC motor, which is coupled with a reducer to adjust the speed. The motor transmits power to the roller through a universal joint and transmission rod, ensuring consistent performance in continuous operations.
An alternative option is the adjustable-speed DC motor, which simplifies the transmission mechanism, offering greater flexibility and ease of speed adjustments. This drive method is particularly useful for operations requiring variable speeds.
In terms of layout, seam welding machines may use either the upper electrode, the lower electrode, or both to drive the rollers. Typically, the upper electrode is driven, as it provides more control over the welding process.
Two common drive methods for roller electrodes are the knurled wheel and gear drive. The knurled wheel system uses friction to rotate the roller electrode by contacting the electrode’s periphery. This ensures a constant linear speed, even as the electrode wears down. The gear drive, on the other hand, uses a gear system with variable speeds. As the roller diameter wears, the speed can be adjusted to maintain consistent linear motion.
MC
Why Choose Us
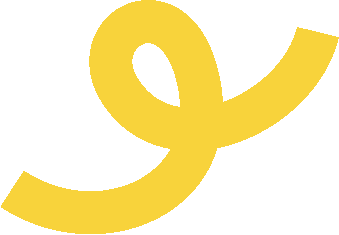
With over a decade of experience in the welding and industrial equipment industry, we are your trusted partner for high-quality welding roller racks and seamless welding solutions. Our products are designed to provide durability, precision, and efficiency, ensuring that your operations run smoothly.
We offer customized solutions tailored to your specific needs, ensuring you get the best performance out of your equipment. Our advanced testing and quality assurance processes guarantee that every machine meets the highest industry standards. Plus, we provide 24/7 online support and a one-year warranty, ensuring you have the assistance you need whenever you need it.
Choose us for reliable, high-performance welding equipment that is backed by years of expertise and a commitment to excellence. Reach out today to learn more or place an order for your next welding project.