

Choosing the Right Gas for CNC Plasma Cutting
Release Time : 2024-12-03 View Count : 次In CNC plasma cutting, the gas used plays a significant role in determining cutting efficiency, speed, and quality. The right choice of gas depends on the material being cut, the thickness of the material, and the specific cutting requirements. Each gas type has unique properties that can enhance or limit cutting performance. This article will explore the various gases commonly used in CNC plasma cutting and how they affect the cutting process.In CNC plasma cutting, the gas used plays a significant role in determining cutting efficiency, speed, and quality. The right choice of gas depends on the material being cut, the thickness of the material, and the specific cutting requirements. Each gas type has unique properties that can enhance or limit cutting performance. This article will explore the various gases commonly used in CNC plasma cutting and how they affect the cutting process.
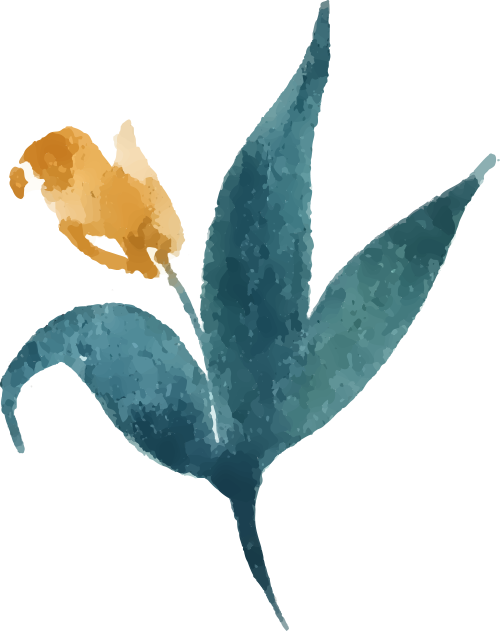
How Gas Affects Cutting Performance
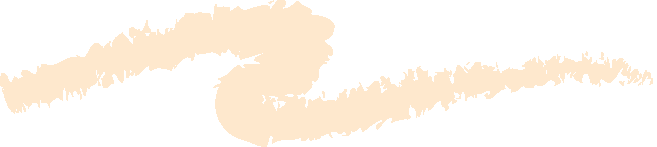
How Gas Affects Cutting Performance
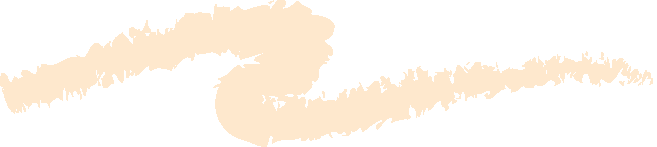
CNC plasma cutting machines require gases with higher no-load and working voltages. Gases like nitrogen, hydrogen, and air, which have high ionization energy, increase the voltage needed to stabilize the plasma arc. This rise in voltage leads to an increase in arc enthalpy, which improves the cutting power. When the gas flow rate is increased, along with a reduction in jet diameter, the plasma arc becomes more focused, leading to faster cutting speeds and better quality cuts.
Hydrogen is often mixed with other gases to improve cutting performance. For example, a mixture like H35, which contains 35% hydrogen and the remainder argon, is known for its strong cutting ability. Hydrogen helps to significantly increase the arc voltage, boosting the enthalpy of the plasma jet and improving the cutting power when combined with argon.
Oxygen is commonly used for cutting low-carbon steel due to the high-temperature and high-energy plasma arc it produces. This arc allows for faster cutting speeds compared to other gases. However, when using oxygen, it is essential to use electrodes that are resistant to high-temperature oxidation to ensure a longer lifespan.
Air is one of the most cost-effective options, as it consists of approximately 78% nitrogen and 21% oxygen. The oxygen content in air helps accelerate cutting speed, particularly when working with low-carbon steel. However, using air for cutting can lead to problems like slag formation, oxidation, and the potential buildup of nitrogen, all of which can impact cutting quality. Additionally, the lifespan of the nozzle and electrode may be reduced when using air, which can increase overall maintenance costs.
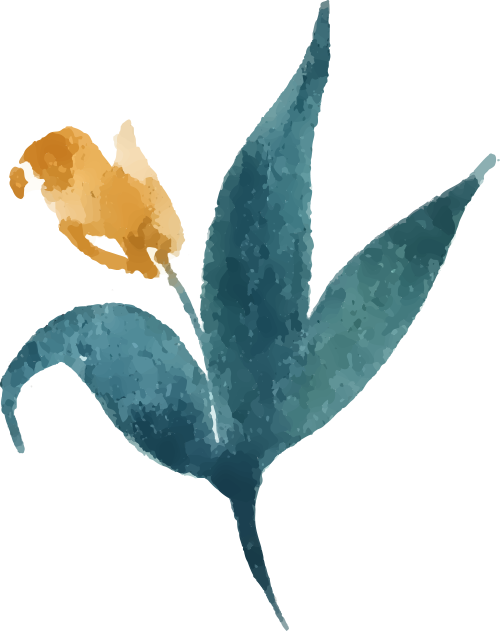
Gas Selection for Different Materials
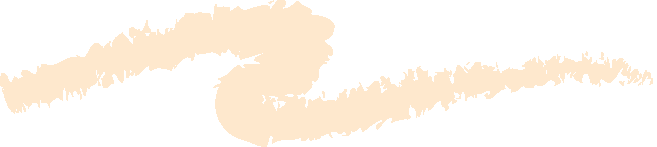
Gas Selection for Different Materials
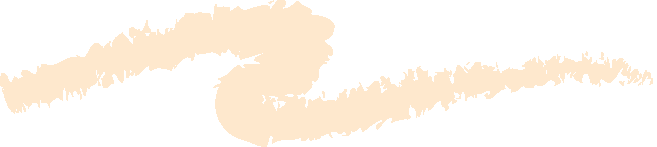
Nitrogen is another widely used gas in CNC plasma cutting. It offers excellent arc stability and higher jet energy compared to argon, particularly under high voltage conditions. Nitrogen is often used for cutting materials like stainless steel and nickel-based alloys. It also minimizes dross formation, which can improve the cut quality.
Argon, on the other hand, is a less reactive gas and offers excellent stability during cutting. While argon plasma arcs have a lower voltage and enthalpy, limiting their cutting capacity, they are ideal for applications requiring stable cutting with minimal electrode wear. However, when compared to air, argon cutting is less effective, and the cutting thickness is typically reduced by about 25%. Additionally, argon tends to produce more dross due to its higher surface tension in the molten metal.
For different cutting applications, it’s important to select the right gas based on the material and thickness being worked on. For example, air or nitrogen are often used for high-speed cutting of carbon steel, while oxygen is preferred for low-carbon steel. Hydrogen, when mixed with other gases, is particularly useful for cutting thicker materials or when high-performance cutting is required.
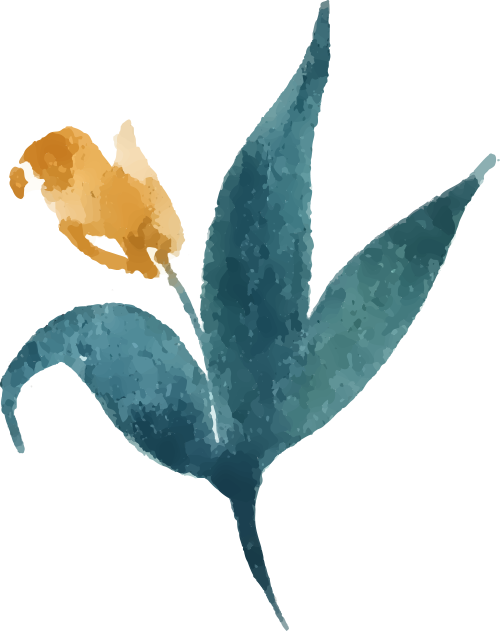
Optimizing Gas Selection for Better Results
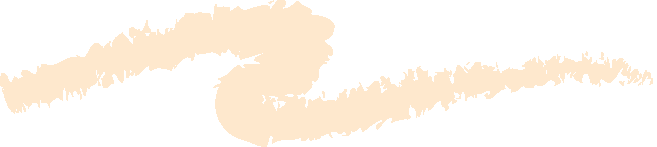
Optimizing Gas Selection for Better Results
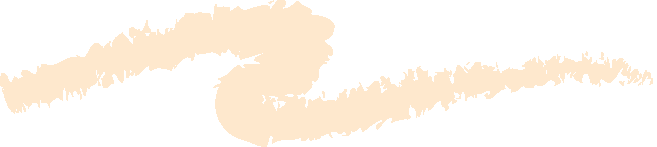
The gas selected for CNC plasma cutting plays a vital role in the overall cutting process. It affects factors such as cutting speed, quality, and the lifespan of components like electrodes and nozzles. By understanding the properties of each gas and how it interacts with different materials, you can make an informed choice to optimize cutting performance and reduce operating costs.
Whether you're using oxygen, nitrogen, hydrogen, or air, the right gas selection will help you achieve cleaner cuts, improve productivity, and extend the life of your plasma cutting equipment. Consider the material, thickness, and cutting speed required for your specific application to determine the best gas for your CNC plasma cutting machine.