

Introduction to Sheet Metal Equipment Structural Design
Release Time : 2024-11-26 View Count : 次Sheet metal processing is a versatile cold-working method for metals, typically under 6mm in thickness. This process involves various techniques, including shearing, punching, cutting, folding, welding, and riveting. A key characteristic of sheet metal parts is that their thickness remains consistent across the entire component. This feature makes sheet metal processing particularly useful in creating a wide range of products, including both simple and complex parts. In this article, we explore the fundamental aspects of the structural design for sheet metal equipment, focusing on design processes, material selection, and considerations for hole structure design.
Sheet Metal Equipment Structural Design Process
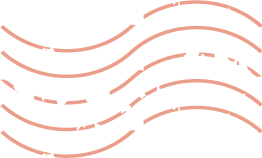
Sheet Metal Equipment Structural Design Process
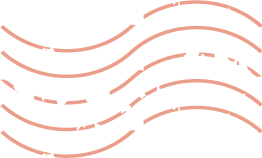
Sheet metal is often deformed through manual processes or die stamping methods to achieve the desired shape and size. For more complex parts, additional steps such as welding or light machining may be employed. Examples of sheet metal parts include everyday household items like chimneys, iron barrels, fuel tanks, ventilation ducts, and funnels, as well as components for electrical cabinets, computer cases, automobile bodies, and specialized equipment enclosures.
The design of sheet metal parts is generally more flexible compared to other equipment types. There are no rigid structural requirements; instead, the design is based on the product's specific needs. While the design must meet functional requirements, it also needs to be easy to manufacture, cost-effective, and aesthetically pleasing. For instance, the door of an electrical cabinet could be either external or built-in, depending on the design requirements. External doors generally require thicker materials and reinforcements to ensure strength, while built-in doors can use thinner materials. This flexibility in design is one of the distinctive features of sheet metal equipment, making it both a challenge and an advantage in the design process.
Key Design Guidelines and Considerations for Sheet Metal Equipment
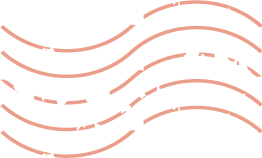
Key Design Guidelines and Considerations for Sheet Metal Equipment
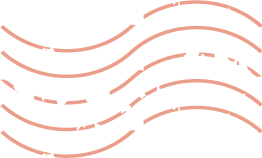
When designing sheet metal equipment, there are several important factors to consider, especially with regard to the materials used and the methods of creating holes in the metal. Proper material selection is essential not only for ease of processing but also to ensure that costs are kept low without compromising strength and durability. In order to optimize material utilization, it's best to avoid using more than three different plate thicknesses in a single structure. For parts that require higher strength, thin plates can be reinforced with ribs to enhance strength without increasing material thickness. Additionally, the dimensions of the parts should never exactly match the outer dimensions of the raw material, as commercially available plates are rarely perfectly square. Such an alignment could result in errors during processing, affecting the final product's fit and function.
For non-sprayed plates that require a decorative surface, it's essential to consider the direction of the grain in the sheet material. If the part is non-exposed, using alternative materials or protective coatings can help reduce unnecessary processing, lowering costs. For exposed parts that will require finishing, choosing the right material with an appropriate grain direction ensures both aesthetic appeal and processing efficiency.
Another important aspect of sheet metal design is the creation of holes. Holes are commonly needed for assembly, ventilation, or other functional purposes. However, the placement and design of these holes must be carefully considered to prevent difficulties in processing and ensure the integrity of the part. For example, square holes should not be placed at the root of a bend, as the bending process can deform the hole. This can lead to increased difficulty in processing and compromise the part's functionality. Furthermore, there are different methods for creating screw holes, such as direct tapping, flanged tapping, riveting nuts, and spot-welding nuts. The choice of method depends on the plate's thickness and the size of the screw hole, with each method offering advantages for different design requirements.
Optimizing Sheet Metal Design for Performance and Efficiency
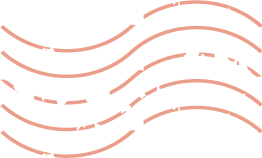
Optimizing Sheet Metal Design for Performance and Efficiency
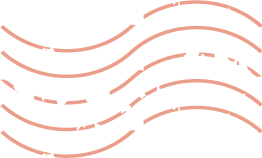
The structural design of sheet metal equipment is intricately linked to the production process. As automation in sheet metal fabrication continues to improve, it is important for designers to stay updated on new techniques and innovations. By understanding and applying these advances, sheet metal designs can be optimized for both product functionality and manufacturing processes. This not only ensures high-quality products but also reduces production costs, enhancing a company's competitiveness in the industry.
At MC, we specialize in delivering customized sheet metal equipment solutions tailored to the unique needs of our clients. With over ten years of experience, advanced testing methods, and a commitment to quality, we are here to support you in achieving the best sheet metal solutions for your business.