

Detecting Weld Quality in Straight Seam Welding Machines
Release Time : 2024-10-22 View Count : 次In industrial production, straight seam welding machines play a critical role in manufacturing metal pipes, which are extensively used across industries such as petroleum, natural gas, chemicals, and construction. The quality of welds produced by these machines directly impacts the safety and durability of the pipelines. Ensuring high-quality welds and accurately identifying defects like incomplete penetration, cracks, slag inclusions, and undercuts is essential for manufacturers to maintain reliable and long-lasting products. Below, we will discuss effective methods for evaluating the weld quality of straight seam welding machines.
Appearance Inspection of Welds
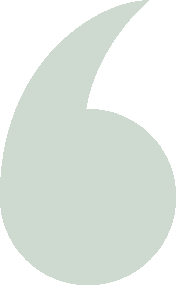
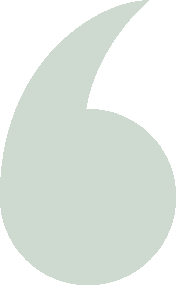
MC
Appearance Inspection of Welds
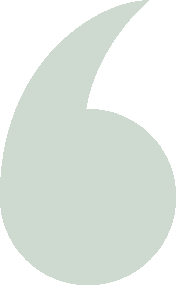
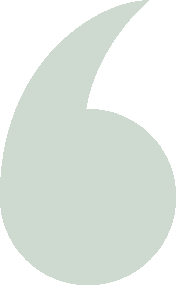
MC
Appearance inspection is the initial step in assessing the weld quality produced by straight seam welding machines. This process involves visually examining the welds, either with the naked eye or with tools such as magnifying glasses. The goal is to confirm that the welds are flat, smooth, and free from any visible defects, such as cracks, pores, and slag inclusions.
When inspecting welds produced by straight seam welding machines, particular attention should be given to the transition between the weld and the parent material on both sides. It is essential to ensure there are no undercuts, as these can compromise the weld's strength. Identifying any irregularities during this stage can prompt further, more detailed testing.
Nondestructive Testing Methods
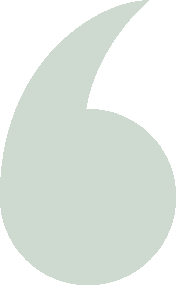
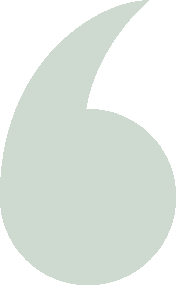
MC
Nondestructive Testing Methods
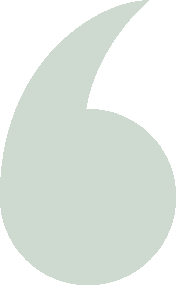
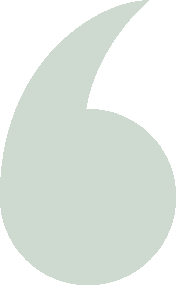
MC
Nondestructive testing (NDT) is a key aspect of quality control for straight seam welding machines. It allows for the detection of internal defects without damaging the welds, providing a comprehensive assessment of weld integrity. Various NDT methods are employed, including ultrasonic testing, radiographic testing, magnetic particle testing, and penetration testing.
For straight seam welding machines, ultrasonic testing (UT) is particularly recommended due to its high sensitivity. This method is capable of detecting even minor internal defects, which is critical for ensuring the overall quality of the welds. In ultrasonic testing, ultrasonic waves are transmitted through a probe, and the reflected waves are analyzed to determine the presence, location, and size of internal defects.
This method is generally preferred over radiographic testing because it is faster, safer, and adaptable to various industrial environments. Although radiographic testing can effectively detect internal defects, it involves the use of radiation, making the process slower and requiring strict environmental controls. Magnetic particle testing and penetration testing, on the other hand, are mainly suited for surface defects and are less frequently used for straight seam welds, where internal defect detection is often a priority.
Ultrasonic Testing Instruments
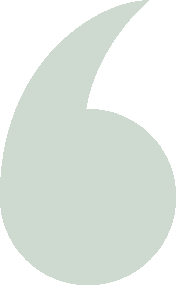
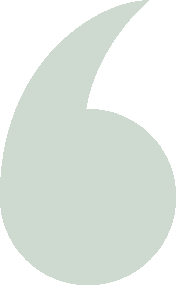
MC
Ultrasonic Testing Instruments
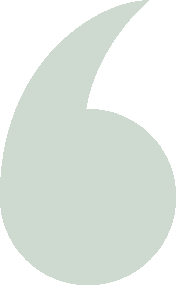
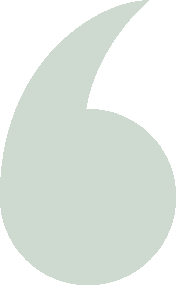
MC
To evaluate the welds produced by straight seam welding machines, ultrasonic flaw detection can be performed using two primary types of equipment: portable ultrasonic flaw detectors and automatic ultrasonic flaw detection systems.
Portable ultrasonic flaw detectors are ideal for manual inspections, providing flexibility and ease of use. These devices are compact, easy to carry, and versatile, but they require skilled operators to interpret the results accurately. This makes them suitable for smaller-scale operations or scenarios where versatility is essential.
For larger production volumes, manufacturers may opt for automatic ultrasonic flaw detection equipment. These systems are designed to offer a high degree of automation, enabling rapid and efficient inspection of welds with minimal manual intervention. Although more expensive than portable devices, automatic systems can process large batches quickly, making them ideal for manufacturers using straight seam welding machines in high-volume production environments.
Using Automatic Flaw Detection Equipment
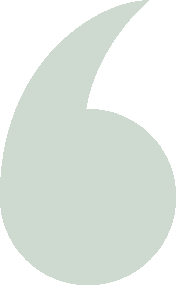
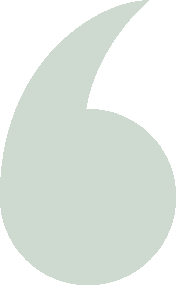
MC
Using Automatic Flaw Detection Equipment
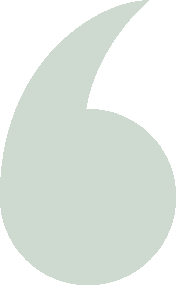
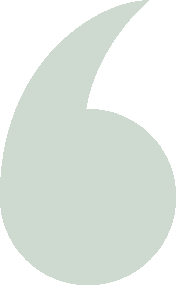
MC
The use of automatic ultrasonic flaw detection equipment involves advanced systems that typically feature an 8-channel design. This setup enables comprehensive inspection of both the weld and the adjacent parent material. After the steel pipes undergo water pressure testing, the equipment combines computer control with real-time signal acquisition technology to conduct a detailed analysis of the welds.
The multi-channel digital flaw detector, supported by high-speed computing, automates several critical tasks, ensuring accuracy and efficiency. This equipment can automatically identify defects, evaluate their severity, and record echo amplitudes, all while storing the collected data.
Additionally, the system can generate detailed reports, which can be printed and formatted to meet specific requirements. The high level of automation provided by these systems enables faster, consistent, and more accurate inspections. This ensures that the welds produced by straight seam welding machines meet quality standards across production batches.
Why Choose Us
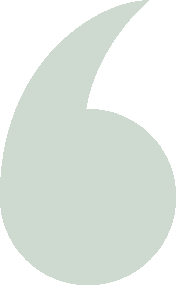
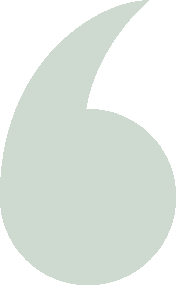
MC
Why Choose Us
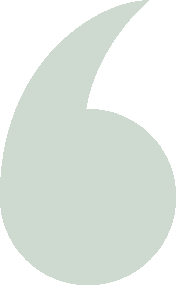
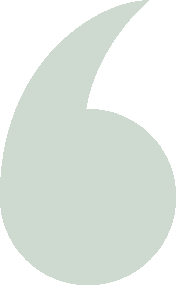
MC
Choosing the right straight seam welding machines is critical for ensuring safety and quality, and we stand out because of our over 10 years of experience, delivering reliable and high-quality solutions. We use advanced testing techniques, including ultrasonic testing, to ensure consistent and precise results, and offer customized machines to meet your specific needs, whether for small-scale or large production. Our products come with a one-year warranty for peace of mind, and our team provides 24/7 support to assist with any technical needs. Partner with us for high-performance, dependable welding solutions.