

Punch Press: Working Principle and Essential Maintenance Guide
Release Time : 2024-09-24 View Count : 次The punch press is an essential machine in the sheet metal stamping industry, widely used for various cold stamping processes such as punching, bending, and shallow drawing. This guide explains the working principle, key components, installation, and daily maintenance of a punch press to ensure optimal performance and longevity.
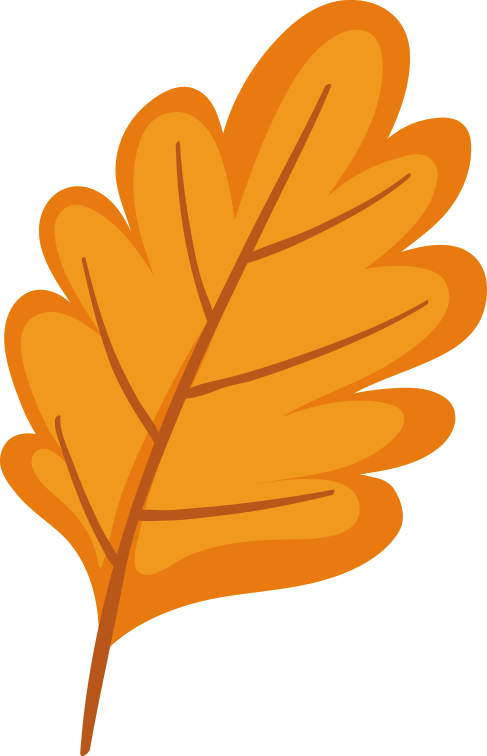
Punch Press Working Principle

Punch Press Working Principle

At the core of the punch press’s operation is a crankshaft and connecting rod mechanism. The motor drives the flywheel, which transmits power through the shaft and small gear to a large gear. This large gear then drives the crankshaft via the clutch, allowing the crankshaft to move the connecting rod, which controls the slider's movement. The slider operates with a fixed number of strokes per minute and follows a specific motion curve.
The punch press consists of several key parts: the bed part, working part, operating part, and transmission part. Each component is critical to the machine’s functionality, ensuring it can perform a variety of cold stamping processes like punching, bending, and shallow drawing with precision and efficiency.
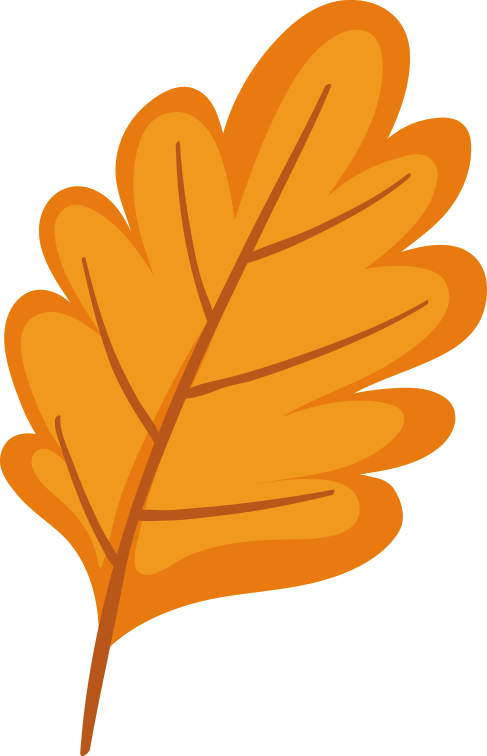
Key Components of the Punch Press

Key Components of the Punch Press

The bed part is constructed from durable cast iron, providing a solid foundation for the punch press. Both the bed and the workbench are cast as one piece, ensuring maximum stability during operation.
The clutch controls the motion of the machine. When the press is idle, the cam of the manipulator keeps the crankshaft idling by pushing the tail of the turn key, stopping the slider at the top dead center. During operation, the cam opens the turn key, engaging the clutch and allowing the crankshaft to rotate, thus moving the slider up and down.
In the slider, a pedal-type safety device ensures the press is protected from overloads. The safety device is easily accessible via a square cover on the front of the machine, making replacement quick and simple when needed.
An eccentric brake band is located at the left end of the crankshaft. When the clutch is disengaged, the brake band overcomes the slider's inertia, ensuring that the crankshaft stops precisely at the top dead center for maximum safety and accuracy.
The manipulator controls the clutch’s engagement and disengagement, allowing for either single or continuous strokes during operation. By adjusting the connection position of the manipulator pull rod, you can easily switch between these two modes depending on the task at hand.
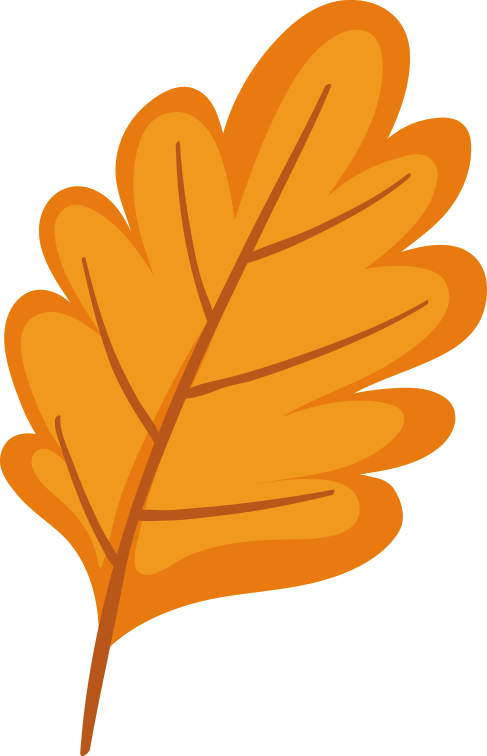
Installation of the Punch Press

Installation of the Punch Press

Proper installation is crucial for optimal performance. Once the punch press is leveled, anchor bolts should be installed, and concrete poured to secure the foundation. After the concrete is completely solidified, the nuts on the anchor bolts must be tightened evenly, and the levelness of the workbench should be checked using a level. It’s important to ensure the ground wire is properly connected.
Before operating the punch press, ensure that the foundation is fully solidified. Clean the surface of the machine using kerosene to remove any anti-rust grease. Be cautious not to damage the paint during cleaning, and frequently clean the oil holes, oil circuits, and lubrication points. Avoid using metal or abrasive cloth when scrubbing to protect the surface.
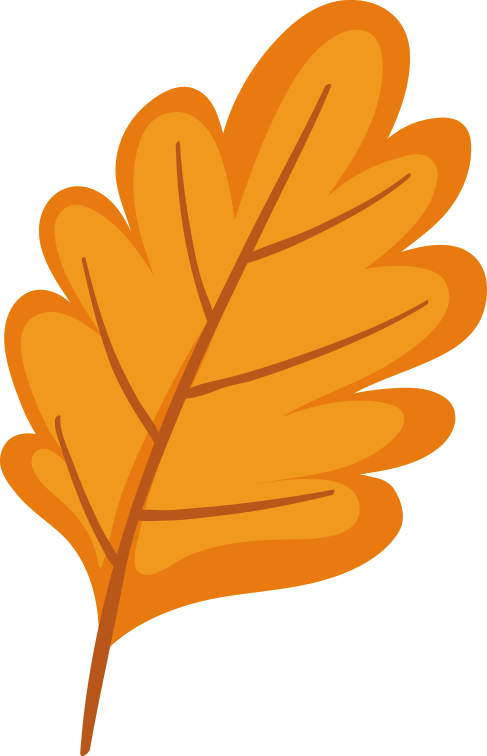
Daily Maintenance of the Punch Press

Daily Maintenance of the Punch Press

Daily maintenance is essential to keep the punch press operating smoothly and safely.
Before starting work, clear the work area and remove any unnecessary items. Check that all friction parts are properly lubricated and inspect the die for any cracks, dents, or signs of wear. Ensure that the clutch is disengaged before starting the machine, and test the brake band, clutch, and manipulator by performing a few test strokes.
During operation, regularly lubricate the machine using an oil gun. If a workpiece becomes stuck on the die, stop the press immediately and resolve the issue. Remove waste materials from the work surface using hooks or other tools—never use your hands. For shallow stretching work, make sure the sheets are clean and well-lubricated. Avoid placing your feet on the manipulator pedal unnecessarily to prevent accidental operation. Always be vigilant for abnormal sounds or malfunctions, such as free-falling sliders or poor-quality finished products, and stop the machine if needed.
After work, disengage the clutch, stop the motor, and clean up the work area. Properly store tools and stamping parts, clear away metal cuttings, and wipe down the press. Apply anti-rust oil to the die edges and any unpainted parts to prevent corrosion.
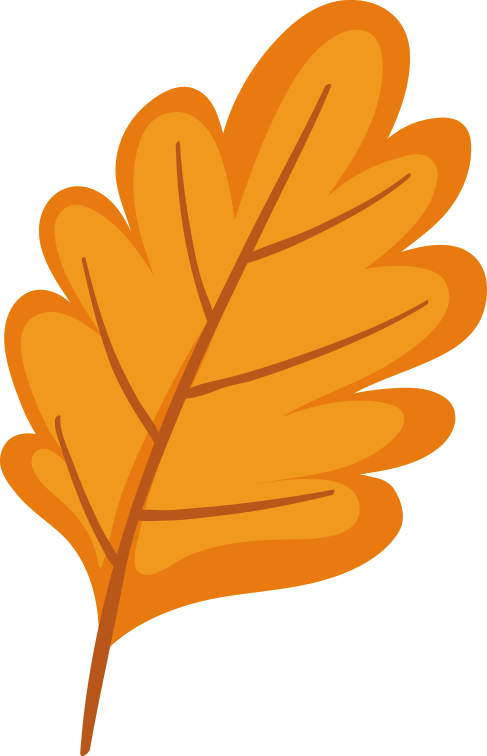
Why Choose Us for Your Punch Press Needs?

Why Choose Us for Your Punch Press Needs?

With over ten years of experience in providing high-quality industrial machinery, we pride ourselves on delivering reliable and efficient punch presses tailored to meet your specific requirements. Our J23-25t punch press is engineered for durability, precision, and versatility, capable of handling a wide range of cold stamping processes such as punching, bending, and shallow drawing.
At our company, we offer more than just machinery. Each machine comes with a one-year warranty and customized service options, ensuring you have the support and flexibility needed for your operations. Our punch presses are built with the highest standards in mind, ensuring long-lasting performance and productivity.
If you’re looking for a punch press that delivers both quality and reliability, we invite you to place an order with us today. Our team is ready to provide you with expert service, guidance, and equipment that will exceed your expectations.