

What is the Process of Flanging? A Detailed Overview
Release Time : 2024-08-13 View Count : 次Flanging, a crucial process in metal forming, involves the creation of a flange on the edge of a workpiece. This method is essential in various industrial applications, including the manufacturing of pipes, tubes, and other cylindrical objects. Flanging machines, which can be manual or automatic, play a significant role in ensuring that the edge forming is beautiful, the quality is reliable, the production efficiency is high, and the operation is convenient. This article delves into the flanging process and the advantages of using specialized edging machines.
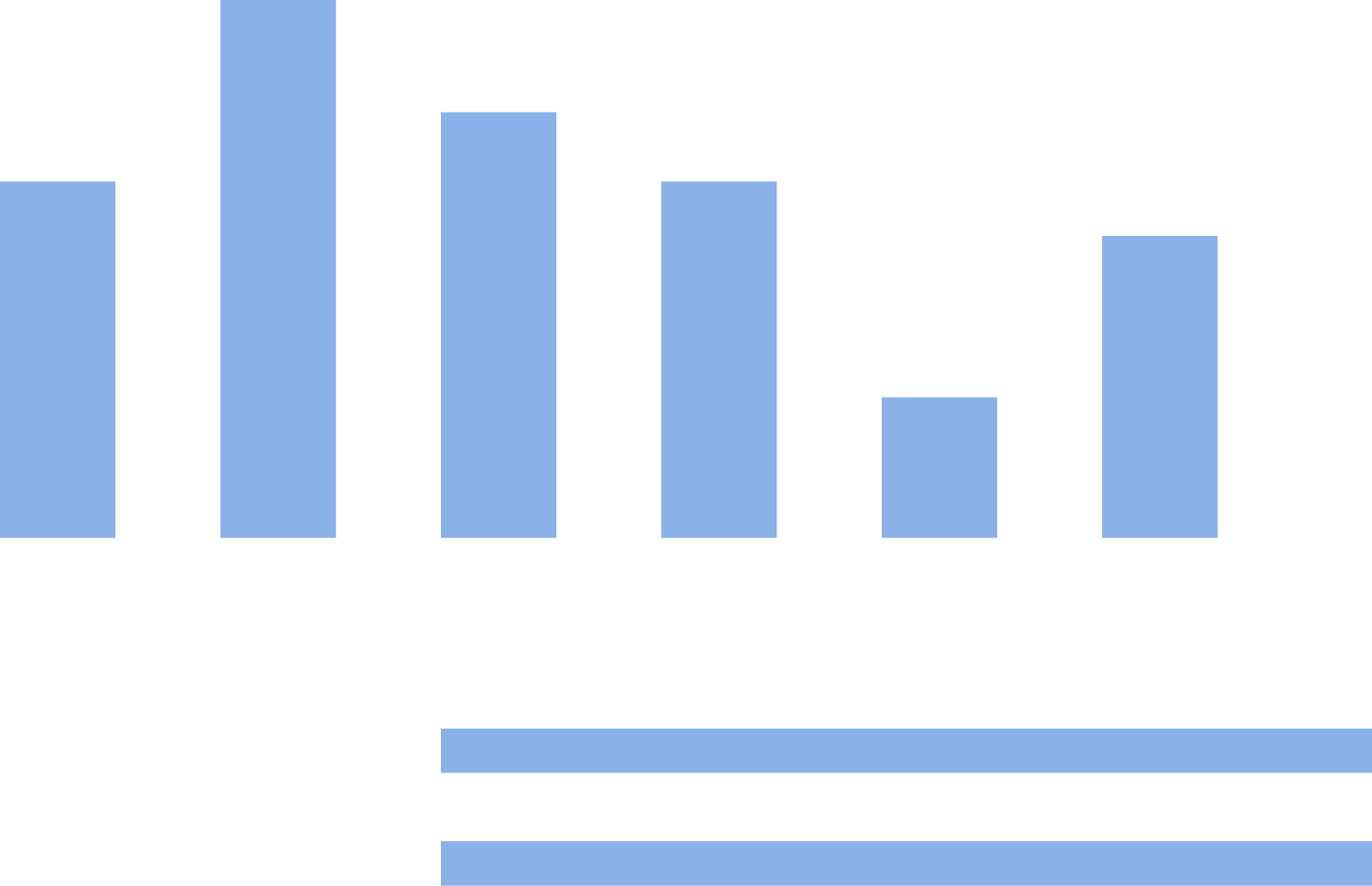
The flanging process begins with the placement of a metal sheet or pipe onto the flanging machine. The machine applies pressure to the edge of the workpiece, bending it to form a flange. This flange can serve multiple purposes, such as providing a lip for welding, enhancing the structural integrity of the piece, or facilitating the attachment to other components.

Manual Edging Machines
- Operation: Manual machines require the operator to control the bending process, ensuring the flange is formed correctly.
- Advantages: These machines are simpler to operate and maintain, making them suitable for smaller workshops or for tasks requiring high precision.
- Disadvantages: The manual process can be slower and more labor-intensive compared to automatic machines.
Automatic Edging Machines
- Operation: Automatic machines are equipped with computerized controls that automate the flanging process, allowing for high-speed production with minimal human intervention.
- Advantages: These machines offer higher production efficiency, consistent quality, and are easier to operate, making them ideal for large-scale manufacturing.
- Disadvantages: They require a higher initial investment and more sophisticated maintenance.
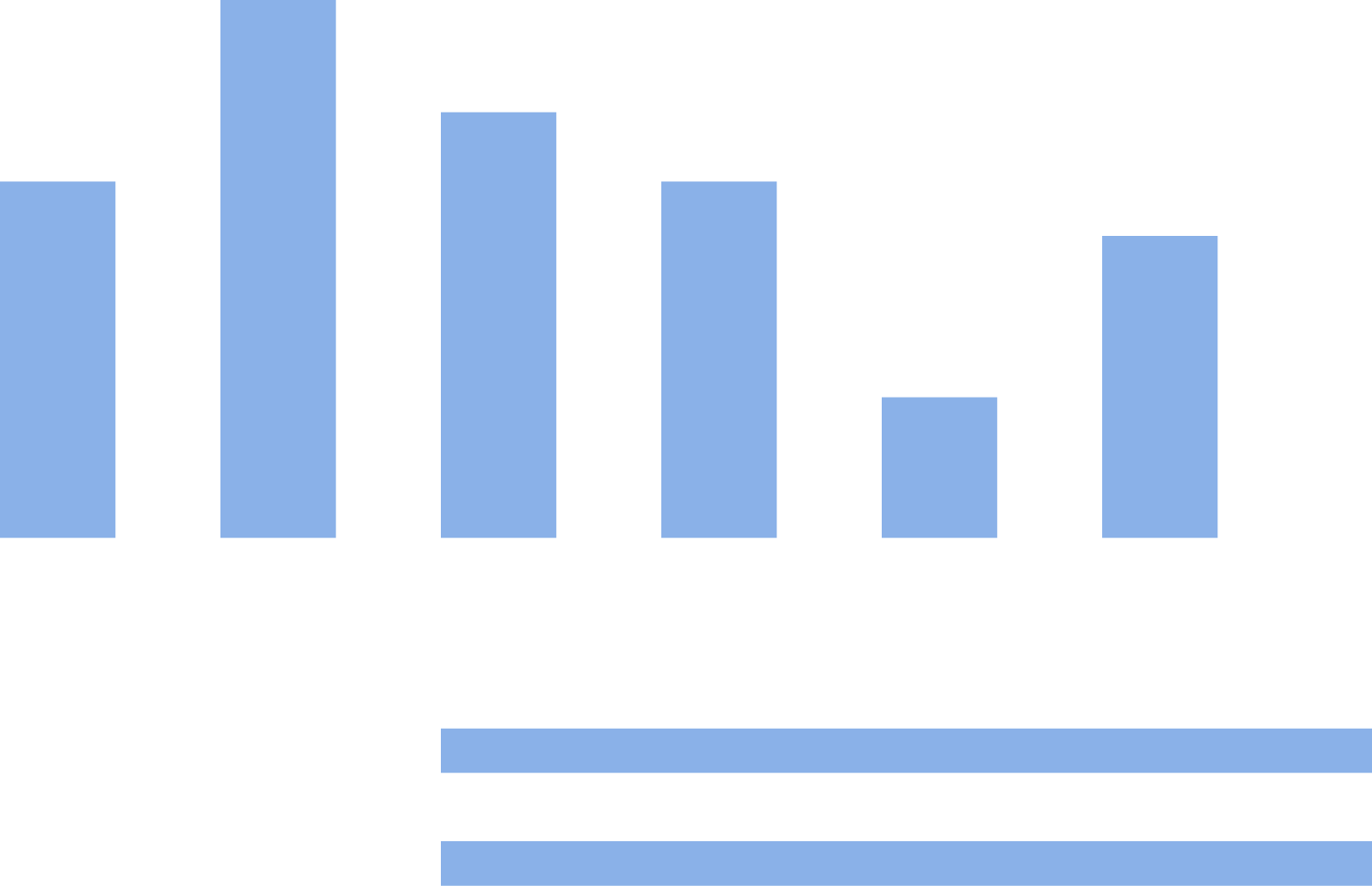
- High Quality and Consistency: The edge forming is precise, resulting in fewer defects and a high-quality finish.
- Increased Production Efficiency: Automated systems significantly speed up the production process, reducing downtime and increasing output.
- Ease of Operation: Both manual and automatic machines are designed for user-friendly operation, reducing the learning curve for new operators.
- Improved Operating Environment: These machines help create a safer and more efficient working environment, reducing physical strain on operators.
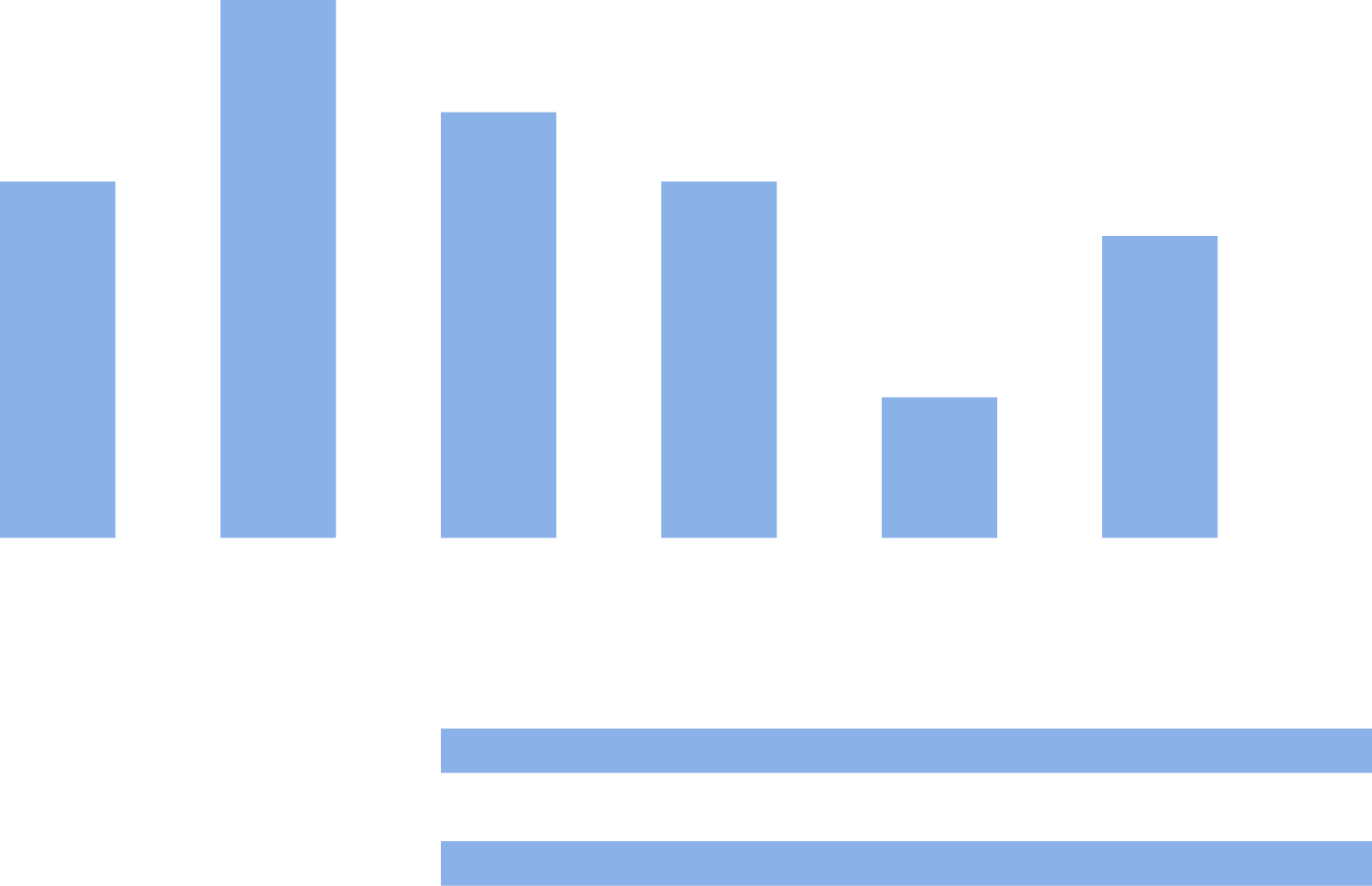
Here are some examples of edging machines and their specifications:
- A simple manual round head forming machine ideal for small-scale operations.
- Suitable for forming both round and conical heads, offering versatility in applications.
- Another variant of the manual round head forming machine with enhanced features for better performance.
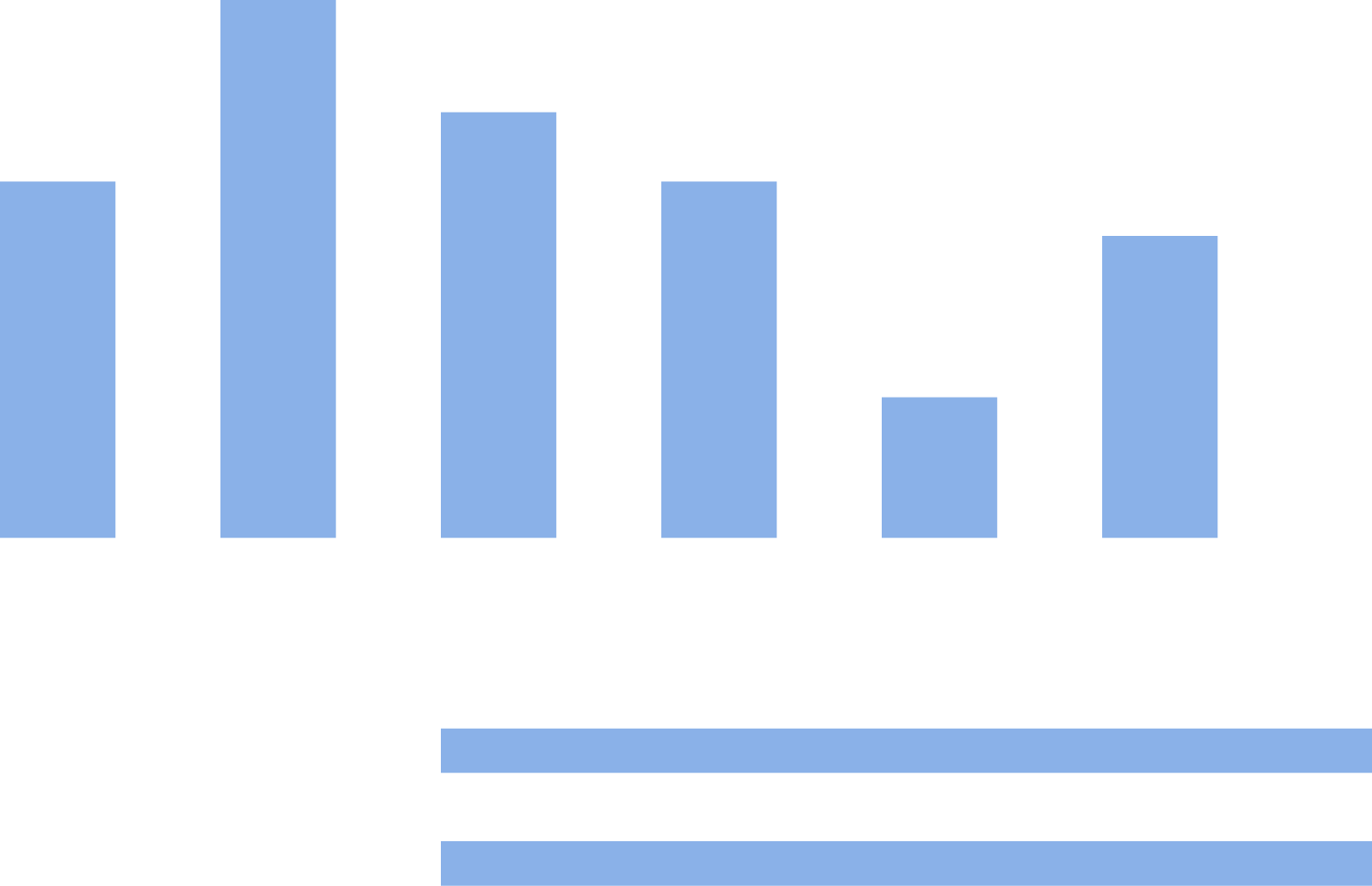
Model | Max. Thickness (mm) | Max. Length (mm) | Advantages | Voltage (V) |
---|---|---|---|---|
MC-0560 | 5 | 600 | Smooth surface, fewer wheel marks, good roundness, high productivity | 220V/60HZ |
MC-05600 | 5 | 6000 | ||
MC-0660 | 6 | 600 | ||
MC-06600 | 6 | 800 | ||
MC-0760 | 7 | 2000 | ||
MC-07400 | 7 | 400 | ||
MC-08400 | 8 | 4000 | ||
MC-08600 | 8 | 6000 | ||
MC-1060 | 10 | 600 | ||
MC-10600 | 10 | 6000 | ||
MC-1190 | 11 | 900 | ||
MC-11500 | 11 | 5000 | ||
MC-1280 | 12 | 800 | ||
MC-12600 | 12 | 6000 |
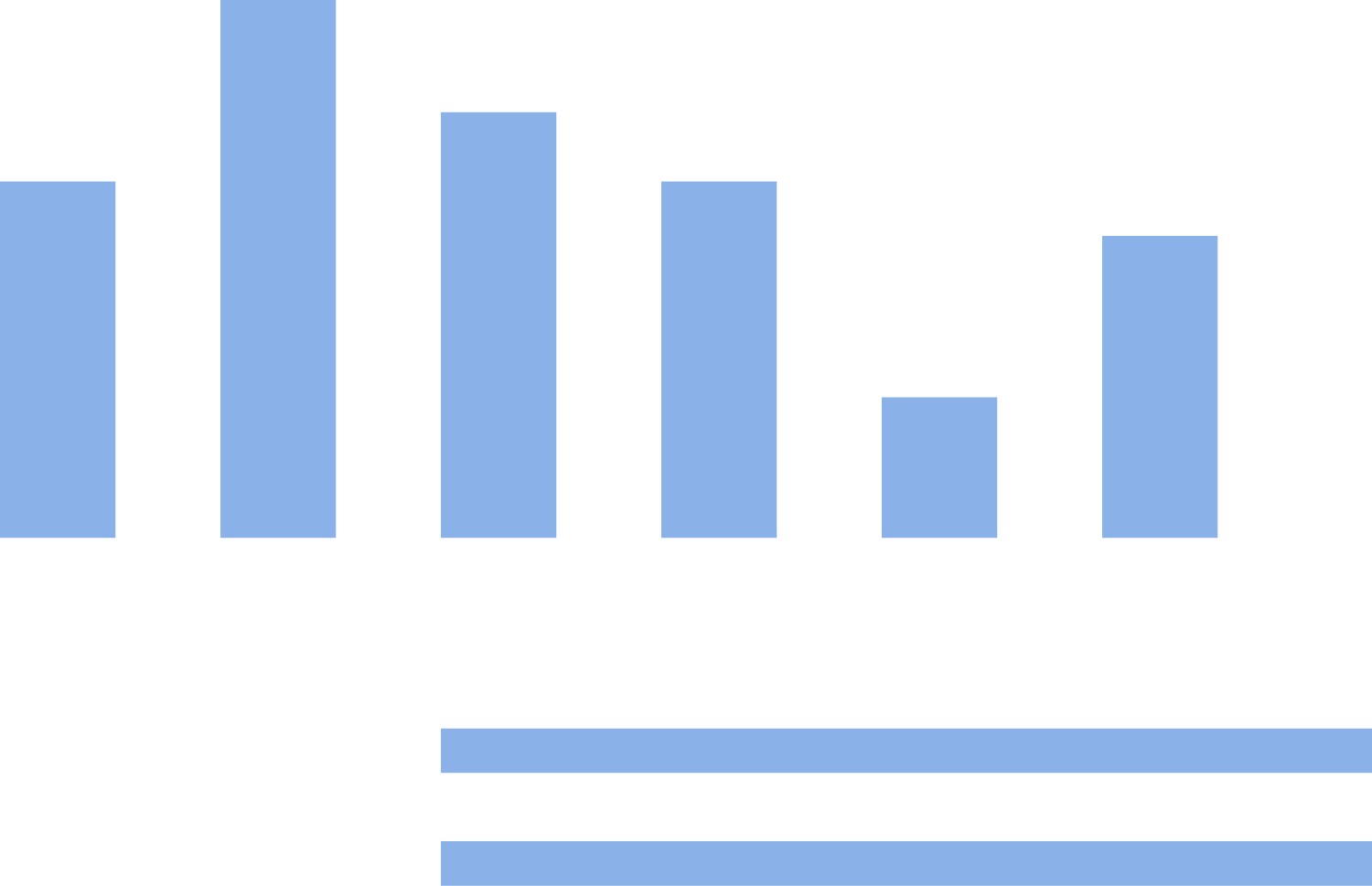
- Max Diameter: Can process workpieces up to ф600mm.
- Material Thickness: Handles carbon steel (4-14mm) and stainless steel (3-10mm).
- Height of Flange Edge: Typically 25mm for 5mm thick material, with adjustments for different materials.
- R Arc: Minimum R arc of the section is R400mm.
- Linear Speed: Plasma cutting and spinning speed ranges from 3m to 8m/min.
- Spinning Speed: For elliptical workpieces, around 25 minutes per piece.
- Operating System: Designed to work 16 hours a day.
- Dimensions: Host dimensions are 4800mm x 1300mm x 1400mm, with a power system dimension of 1600mm x 800mm x 1200mm.
- Power Consumption: Total power is less than 13KW, excluding plasma power supply.
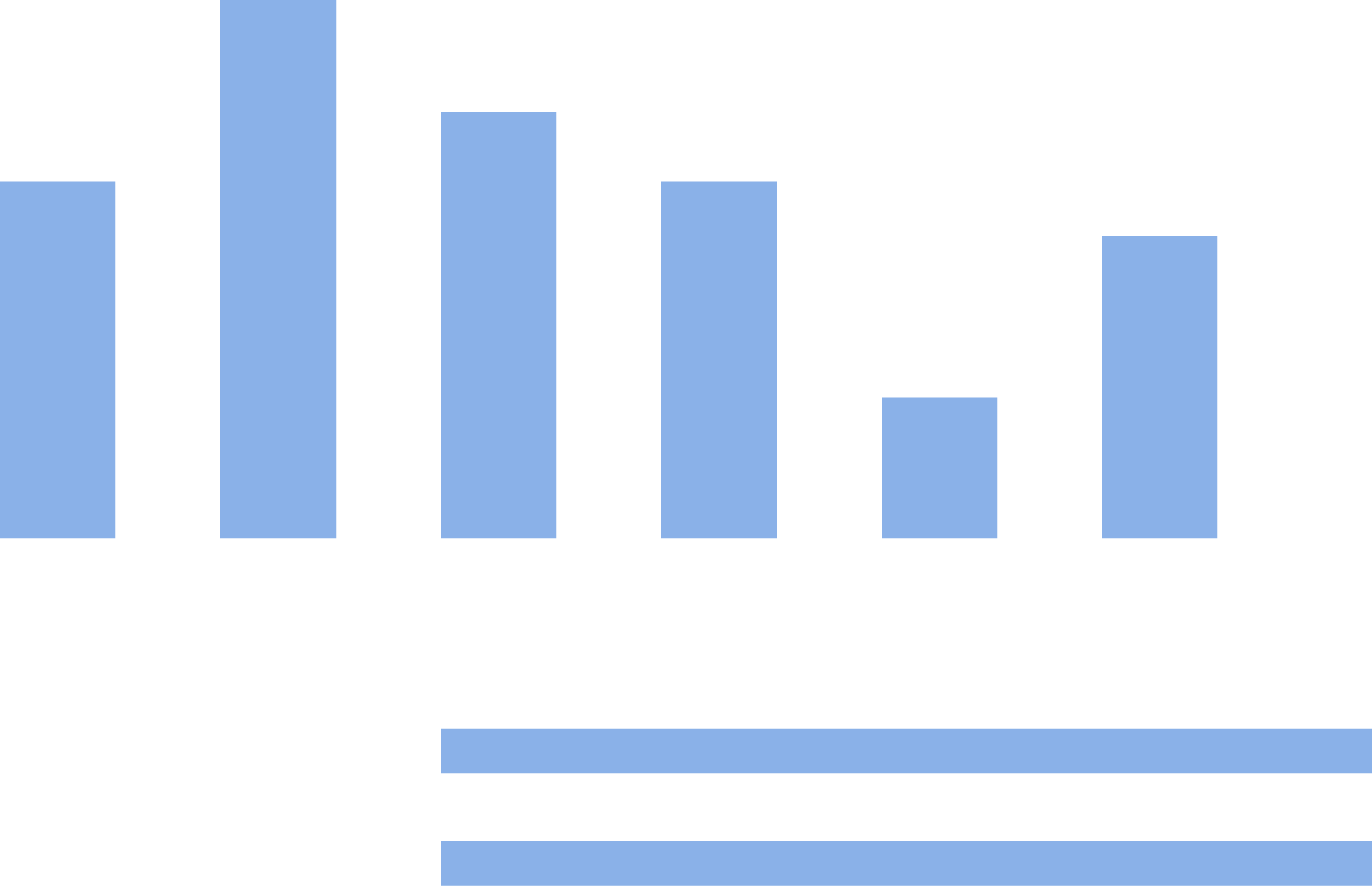
Edging machines are widely used in various industries, including:
- Leisure food factory equipment
- Winery equipment
- Fruit and vegetable processing plant equipment
- Frozen food factory equipment
- Seasoning processing equipment
- Meat processing equipment
- Crimping machines
- Flat-bottle-crimping machines
- Screw machines
- Lathes
- Cylinder crimping machines
- Beer can crimping machines
- Oil cabinet head crimping machines
The machine structure typically features symmetrical positioning between the main drive wheel and the passive wheel, ensuring balanced rotation and precise output. This balance is crucial in achieving the desired rolling diameter and maintaining the integrity of the material during the flanging process.
In conclusion, the process of flanging is integral to various manufacturing sectors, providing high-quality edges and efficient production capabilities. Whether opting for a manual or automatic edging machine, understanding the specific needs and capabilities of each model can significantly enhance your production efficiency and product quality.